
Treatments
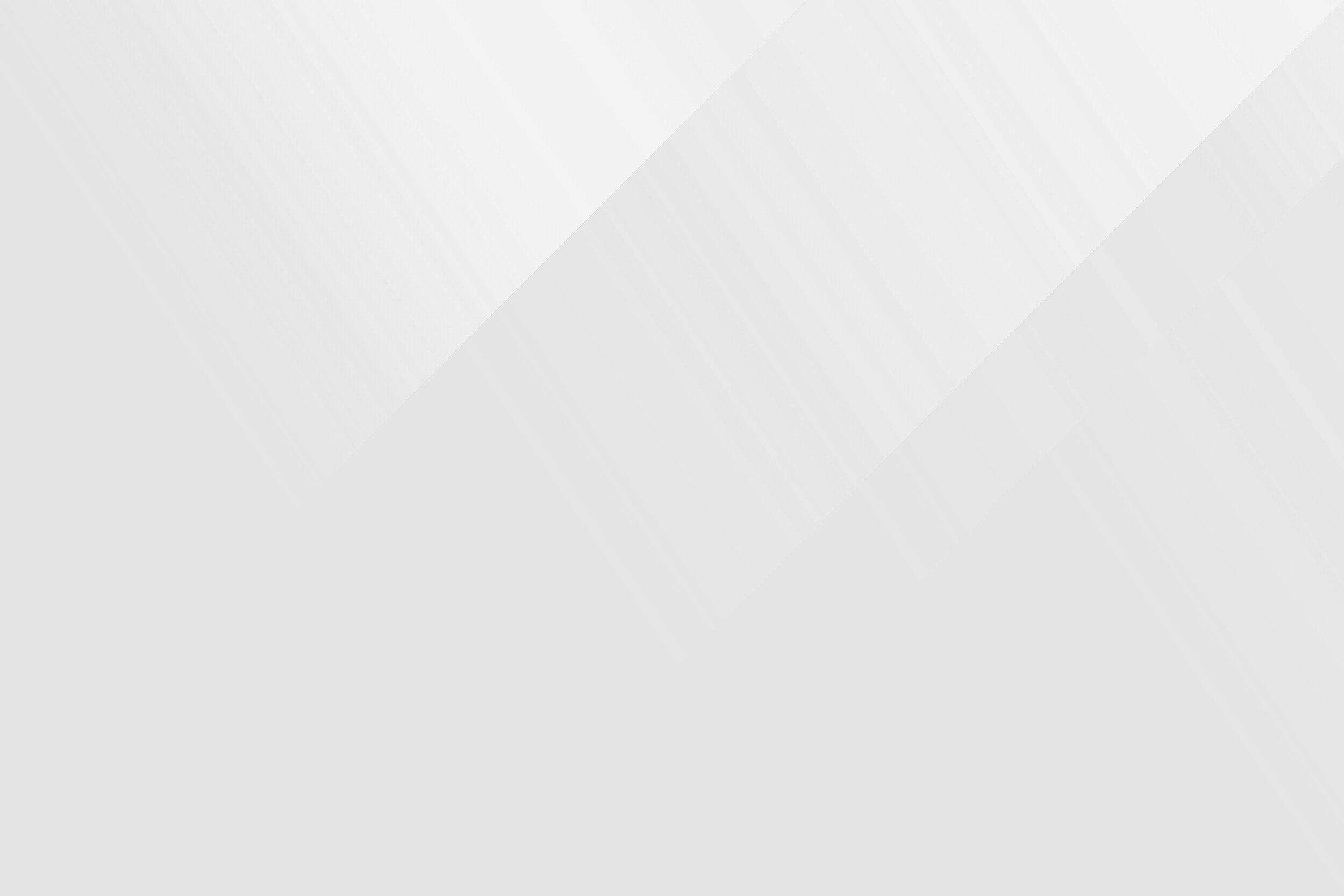
Non Destructive Testing Services
Hardness Testing (Rockwell & Vickers)
We use both the industry recognised Rockwell and Vickers systems for measuring Hardness, the Rockwell Hardness test being the most commonly used. The Vickers Hardness testing method is mostly for small parts or thin sections and uses an optical measurement system to measure the size of the indentation across the diagonals rather than the depth of the indentation.
Conductivity Testing
This is an NDT technique which is used to determine a range of conductivity properties of a metallic part being tested. This can also be used to examine the type of metal or alloy. Conductivity is calculated from the measured resistance and dimensions of the part is like the reciprocal of the electrical resistivity. The testing can be used to examine the type of metal or alloy, type of heat treatment, aging of the alloy, effects of corrosion, heat damage, and temper as well as the hardness of non-magnetic materials. The electrical conductivity test can also be used to verify proper heat treatment if used in conjunction with hardness testing.
Etch Inspection
Acid etch inspection is an NDT technique used to determine whether components have suffered grinding abuse during the manufacturing process. This inspection system uses a systematic sequence of acid etching which will highlight any hard or soft elements produced by poor or inconsistent grinding. Inspection in natural light after these treatments will reveal any defects.
Penetrant Flaw Detection
Used by our highly experienced and fully qualified Level 2 Inspectors this NDT inspection method is used to check surface-breaking defects in all non-porous materials (metals, plastics, or ceramics). In essence a fluorescent penetrant dye is applied to the material surface and allowed to penetrate any flaws on the part. Any excess penetrant is removed and a developer is applied which shows up any defect on the part. The penetrant may be applied to all non-ferrous materials and ferrous materials, although for ferrous components magnetic-particle inspection is often used instead for its subsurface detection capability. PFD is used to detect casting, forging and welding surface defects such as hairline cracks, surface porosity, leaks in new products, and fatigue cracks on in-service components. All treatments, as appropriate have fully signed Level 3 NDT Techniques.
Magnetic Flaw Detection
Our highly experienced and fully qualified Level 2 Inspectors use this NDT inspection method for detecting surface and shallow subsurface discontinuities in ferromagnetic materials such as iron, Nickel and Cobalt and some of their alloys. We have 2 state of the art MFD benches, one using half wave rectification and the other full wave rectification. The process puts a magnetic field into the part which by direct or indirect magnetization. Direct magnetization occurs when the electric current is passed through the test object and a magnetic field is formed in the material. Indirect magnetization occurs when no electric current is passed through the test object, but a magnetic field is applied from an outside source. The magnetic lines of force are perpendicular to the direction of the electric current, which may be either alternating current (AC) or some form of direct current (DC) (rectified AC). The presence of a surface or subsurface discontinuity in the material allows the magnetic flux to leak, since air cannot support as much magnetic field per unit volume as metals. To identify a leak, ferrous particles, either dry or in a liquid suspension, are applied to a part. These are attracted to an area of flux leakage and form what is known as an indication, which is evaluated to determine its nature, cause, and course of action, if any.