
Treatments
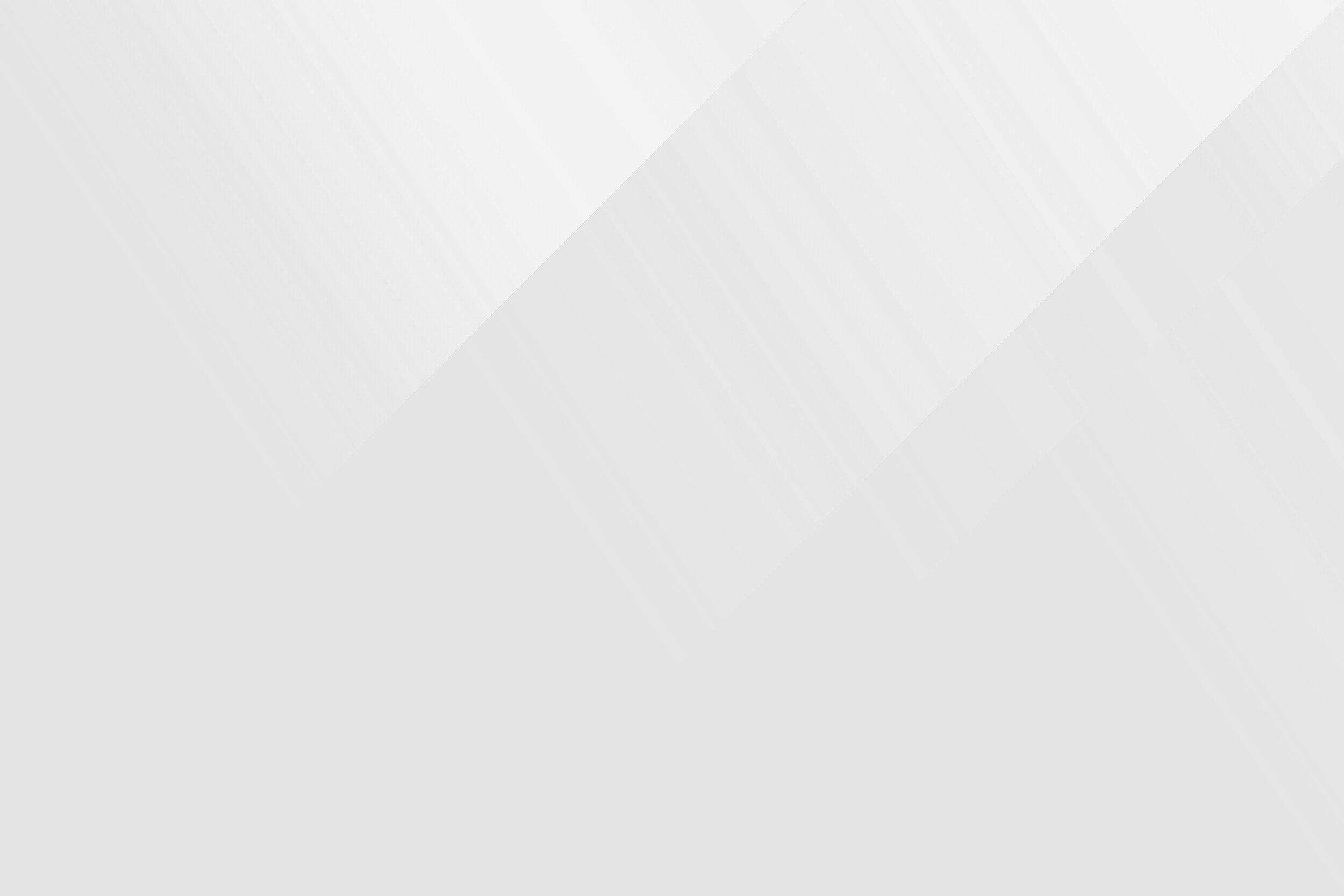
Non Destructive Testing Services
Hardness Testing (Rockwell & Vickers)
We use both the industry recognised Rockwell and Vickers systems for measuring Hardness, the Rockwell Hardness test being the most commonly used. The Vickers Hardness testing method is mostly for small parts or thin sections and uses an optical measurement system to measure the size of the indentation across the diagonals rather than the depth of the indentation
Conductivity Testing
This is an NDT technique which is used to determine a range of conductivity properties of a metallic part being tested. This can also be used to examine the type of metal or alloy. Conductivity is calculated from the measured resistance and dimensions of the part is like the reciprocal of the electrical resistivity. The testing can be used to examine the type of metal or alloy, type of heat treatment, aging of the alloy, effects of corrosion, heat damage, and temper as well as the hardness of non-magnetic materials. The electrical conductivity test can also be used to verify proper heat treatment if used in conjunction with hardness testing.
Etch Inspection
Acid etch inspection is an NDT technique used to determine whether components have suffered grinding abuse during the manufacturing process. This inspection system uses a systematic sequence of acid etching which will highlight any hard or soft elements produced by poor or inconsistent grinding. Inspection in natural light after these treatments will reveal any defects.
Penetrant Flaw Detection
Used by our highly experienced and fully qualified Level 2 Inspectors this NDT inspection method is used to check surface-breaking defects in all non-porous materials (metals, plastics, or ceramics). In essence a fluorescent penetrant dye is applied to the material surface and allowed to penetrate any flaws on the part. Any excess penetrant is removed and a developer is applied which shows up any defect on the part. The penetrant may be applied to all non-ferrous materials and ferrous materials, although for ferrous components magnetic-particle inspection is often used instead for its subsurface detection capability. PFD is used to detect casting, forging and welding surface defects such as hairline cracks, surface porosity, leaks in new products, and fatigue cracks on in-service components. All treatments, as appropriate have fully signed Level 3 NDT Techniques.
Magnetic Flaw Detection
Our highly experienced and fully qualified Level 2 Inspectors use this NDT inspection method for detecting surface and shallow subsurface discontinuities in ferromagnetic materials such as iron, Nickel and Cobalt and some of their alloys. We have 2 state of the art MFD benches, one using half wave rectification and the other full wave rectification. The process puts a magnetic field into the part which by direct or indirect magnetization. Direct magnetization occurs when the electric current is passed through the test object and a magnetic field is formed in the material. Indirect magnetization occurs when no electric current is passed through the test object, but a magnetic field is applied from an outside source. The magnetic lines of force are perpendicular to the direction of the electric current, which may be either alternating current (AC) or some form of direct current (DC) (rectified AC). The presence of a surface or subsurface discontinuity in the material allows the magnetic flux to leak, since air cannot support as much magnetic field per unit volume as metals. To identify a leak, ferrous particles, either dry or in a liquid suspension, are applied to a part. These are attracted to an area of flux leakage and form what is known as an indication, which is evaluated to determine its nature, cause, and course of action, if any.
Electro Plating
Stress relieving & de-embrittlement
High tensile, hardened and spring steels are particularly susceptible to damage by embrittlement when protective electroplated coatings are applied. Various engineering techniques including grinding and machining can create stresses in the surface of a component. Hydrogen can be introduced into components during cleaning, pickling and electroplating processes which can result in a loss of ductility, load carrying ability or cracking of a metal or alloy. Treatments such as Hard Chrome and Copper introduce elements of Hydrogen which render the material brittle. To prevent the failure of these components stress relieving and hydrogen de-embrittlement are an absolute necessity. These low temperature heat treatment processes reduce surface stresses and reduce or eliminate the danger of hydrogen embrittlement. In essence, the components are placed in an oven for several hours depending on the material requirements until the diffused hydrogen has been removed from the material. We have all the facilities to carry out these processes to ensure full compliance to specifications.
Cadmium Plating & Passivation
We are one of the few treatment houses who can offer this very effective surface treatment. It gives exceptional bonding surface for adhesives, such as those used in aircraft manufacture, and is the preferred coating for salt-water environments. The coating is electropositive to iron and has a very low contact potential to aluminium which greatly reduces the risk of corrosion when applied to fasteners in contact with the aluminium skin or frame of an aircraft. The protection of iron and steel is sacrificial in that when applied, the Cadmium Plating corrodes in preference leaving the substrate undamaged even if the coating is scratched.
Hard Chrome
Hard Chrome plating applies thick deposits of Chromium on a base material giving extremely high levels of adhesion. The plating is extremely hard enhancing durability, wear and hardness, but providing low-co-efficient of friction making it ideal when there is metal to metal contact on sliding applications.
Copper Plating (Pyrophosphate Type)
This form of Copper Plating provides high throwing power and ductile copper deposition. As the copper substrate is easy to plate then it is widely used as an undercoat for other deposits. The high throwing power and fast deposition rates of pyrophosphate copper make it a useful stopping off medium for use on steel components which are to be selectively surface hardened by nitriding or carburising.
Silver Plating (Dull)
We only offer Industrial silver plating. It has a number of properties including corrosion resistance, oxidation resistance, great wear resistance, improving solderability of the substrate, exceptional lubricity even at high temperatures, high electrical conductivity and anti-galling due to its low friction properties. Silver plating can also be used to improve paint adhesion and infrared reflectivity, as well as for use in radiation shielding.
Hard Nickel (Sulphamate)
This treatment is deposited for dimensional corrections, abrasion and wear resistance, high efficiency coating and corrosion protection. It is also used as an undercoat for chromium
Stainless Steel Passivation
Passivation is a non-electrolytic finishing process that makes stainless steel more corrosion resistant. The passivation process typically uses nitric or citric acid to remove free iron from the surface. This results in an inert, protective oxide layer that is less likely to chemically react with air and cause corrosion.
Anodising
Sulphuric Anodising & Dyeing
This form of anodising is mainly used for its anti-corrosive properties and is typically 10 – 15µm thick. This finish is can be either clear or we can offer a range of colours giving a more decorative look.
Anodising of Titanium
Used solely on Titanium alloys, by converting a thin surface layer of the titanium to titanium dioxide creates a coating that can be used with solid lubricants for the protection of fasteners against galling and will also protect less noble metals from galvanic corrosion when in contact with titanium. The coating is not highly abrasion resistant.
Hard Sulphuric Anodising & Dyeing
Hard anodising is typically used for wear resistance, corrosion protection and for thermal or electrical insulation hence it can have a thickness between 25 to 50µm thick.
Chromic Anodising
This treatment, due to its thin layer of 1–2µm thickness, it typically used for its anti-corrosion properties with minimal loss of metal section and as a pre-treatment for paint application. The process can also be used for the treatment of riveted and other assembled parts where no risk of corrosion due to entrapped electrolyte can be tolerated.
Alocrom 1200
Alocrom is used to provide levels of corrosion protection, electrical conductivity and paint adhesion.
Paint Finishes
Etch Primer
With our highly trained and experience team we are able to offer many aerospace and defence standard paint schemes.
Etch Primer is a paint that is designed to physically bond itself to the substrate to which it is applied. This is achieved by combining an acid with the paint so that the acid microscopically etches the surface of the substrate, thus forming a physical and chemical bond between the two.
Epoxy Primer
With our highly trained and experience team we are able to offer many aerospace and defence standard paint schemes.
Epoxy primers have excellent adhesion properties and will stick to bare metal, paints, primers and fillers. E
Epoxy Finishes
With our highly trained and experience team we are able to offer many aerospace and defence standard paint schemes.
Epoxy paints provide extremely tough and durable finish
Polyurethane Finishes
With our highly trained and experience team we are able to offer many aerospace and defence standard paint schemes.
Polyurethane paint is a hard-wearing, highly-resistant coating. It is a reaction polymer, a combination of a polyol resin and an isocyanate hardener or curing agent.
Rockhard Varnish
With our highly trained and experience team we are able to offer many aerospace and defence standard paint schemes.
Dry Film Lubricants
We use Molybdenum Disulphide as a dry film lubricant within our processes, providing low friction, high load bearing, chemical, abrasion and corrosion resistance.